- 본 게시글은 Factory Physics(3e, Wallace J. Hopp) 공부 정리글입니다.
- 개인적인 생각과, 책에 서술되지 않은 내용이 추가되었을 수 있습니다.
- 잘못된 이해에서 비롯된 오류는 지적해 주시면 감사하겠습니다.
Is Variability always bad?
The answer is straightforward: variability is typically viewed as something to be minimized. However, it's essential not to lose sight of the core objective of business. When customers demand a new product (such as a car in red or blue), the company must adapt and fulfill those needs, even if it introduces additional variability.
Ultimately, a company exists to generate profit. If expanding product variety leads to increased variability but also boosts revenue to a degree that outweighs the added costs, it can represent a prudent business strategy.
Yet, it's crucial to discern between bad and good variability. The table below outlines examples of both types:
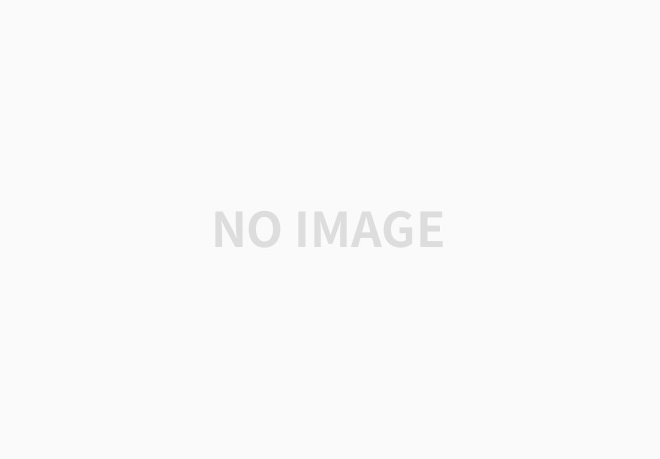
Regardless of whether variability is good or bad in business strategy terms, it causes operating problems and therefore must be managed.
Variability Laws
Law (Variability): Increasing variability always degrades the performance of a production system.
Increasing variability inevitably leads to decreased performance in production systems, regardless of its nature. Thus, reducing variability becomes crucial for enhancing performance. Methods like production smoothing and total quality management are integral to achieving this reduction. These strategies were fundamental to the success of JIT systems. The recognition of variability's impact underscores its significance in operational efficiency. Consequently, managing variability effectively is a cornerstone of production optimization.
Law (Variability Buffering): Variability in a production system will be buffered by some combination of 1. Inventory 2. Capacity 3. Time
This law significantly extends the understanding of variability by highlighting the buffers it creates. It suggests that although variability will inevitably degrade performance, the manner in which it does so can be influenced. Various strategies for managing variability are viable in different business contexts, offering flexibility in coping with its effects.
In my opinion, an example of buffer inventory is the push-pull boundary, which acts as the interface between push-based and pull-based stages in production. This boundary is covered by inventory, serving to regulate the differing speeds of push and pull within the system.
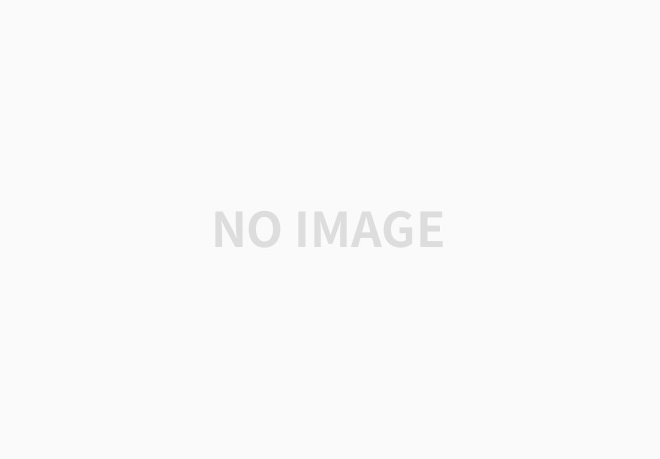
Flexibility
Flexibility in buffering helps reduce variability's effects by allowing buffers to be used in different ways. Unlike fixed buffers, flexible ones can change as needed, making them more available and responsive. This shows how important it is to use flexible buffers to manage variability efficiently.
Corollary (Buffer Flexibility): Flexibility reduces the amount of variability buffering required in a production system.
Flexibility can be integrated into production systems in various ways, such as designing products, facilities, equipment, and managing vendors.
Flow Laws
In this section, we will discuss laws related to material flow, capacity, utilization, and the propagation of variability.
Product Flows
Law (Conservation of Material): In a stable system, over the long run, the rate out of a system will equal the rate in, less any yield loss, plus any parts production within the system
In a stable system, the amount going in shouldn't exceed what the system can handle. However, over time, the system might observe short-term deviations where more material leaves than enters, causing inventory to drop until production stops. This imbalance can't last forever. Additionally, we must consider yield loss (like scrap) and parts production (when one part becomes many). These factors are crucial alongside the basic principle that input equals output.
Capacity
Law (Capacity): In steady state, all plants will release work at an average rate that is strictly less than the average capacity
This law holds significant implications. Achieving 100% utilization of plant resources is impractical, prompting management to decide whether measures like excess capacity, overtime, or subcontracting should be part of a planned strategy or used reactively when conditions become chaotic. Unfortunately, many manufacturing managers overlook this law of Factory Physics, leading them to operate their factories in a perpetual "fire-fighting" mode without realizing it.
Utilization
The buffering law and the VUT equation highlight two primary factors influencing queue time: utilization (u) and variability (v). Among these, utilization has the most pronounced impact. This is because the VUT equation (applicable to single- or multiple-machine stations) features a 1 − u term in the denominator. As utilization u approaches one, cycle time approaches infinity. This principle can be summarized as follows:
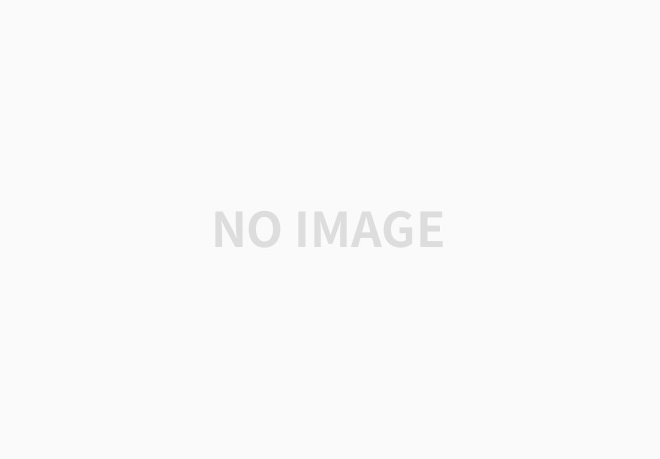
Law (Utilization): If a station increases utilization without making any other changes, average WIP and cycle time will increase in a highly nonlinear fashion.
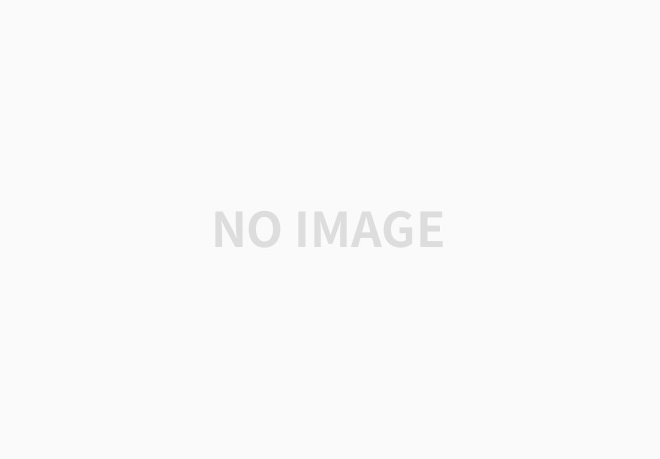
As utilization (u) approaches one, the effect becomes even more pronounced, as illustrated in Figure 9.2. This graph depicts the relationship between cycle time and utilization for two scenarios: one with V = 1.0 and another with V = 0.25, where V represents the variability. Both curves show a significant increase ("blow up") in cycle time as u nears 1.0, but the curve corresponding to higher variability (V = 1.0) demonstrates a faster escalation. Little's law indicates that work-in-progress (WIP) experiences a similar increase as u approaches one.
Batching Laws
There are two main types of batches in manufacturing: transfer batches and process batches.
Transfer batches refer to the accumulation of parts before being moved to the next station. Smaller transfer batches reduce cycle time by minimizing the wait time for batch formation. However, smaller transfer batches also increase material handling, creating a trade-off.
Process batches involve processing multiple transfer batches together. There are two types: sequential and simultaneous. Sequential batches are processed before the workstation changes over to another part or family, while simultaneous batches involve producing multiple parts simultaneously in a workstation. Despite their physical differences, both types of process batches have similar operational effects.
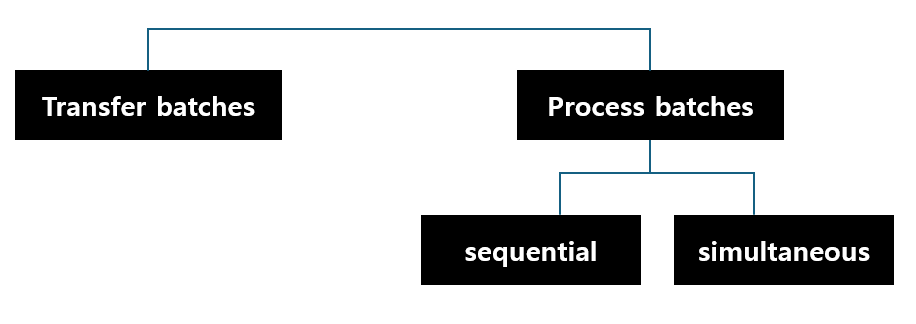
Process Batching
Law (Process Batching): In stations with batch operations or significant changeover times:
1. The minimum process batch size that yields a stable system may be greater than one.
2. As process batch size becomes large, cycle time grows proportionally with batch size.
3. Cycle time at the station will be minimized for some process batch size, which may be greater than one.
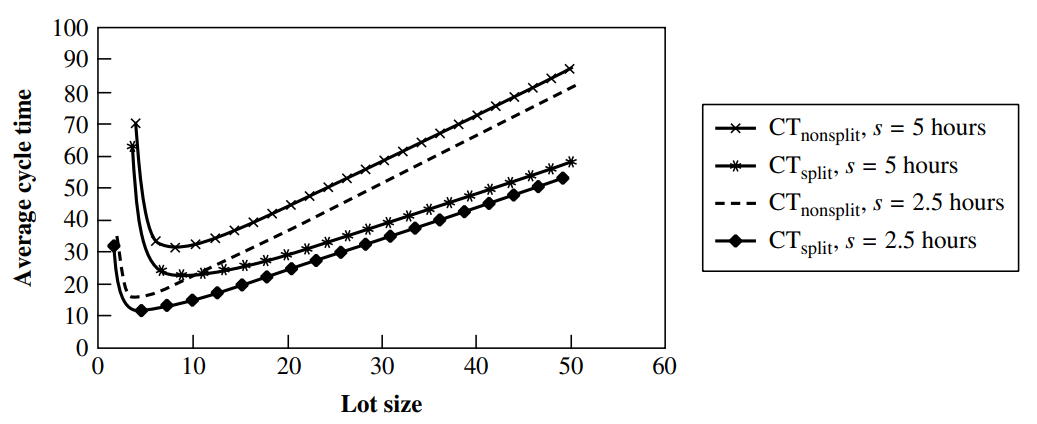
Transfer Batches
Law (Move Batching): Cycle times over a segment of a routing are roughly proportional to the transfer batch sizes used over that segment, provided there is no waiting for the conveyance device.
'공부 정리 > Factory Physics' 카테고리의 다른 글
[Factory Physics] 8. Variability Basics (3) (0) | 2024.02.20 |
---|---|
[Factory Physics] 8. Variability Basics (2) (0) | 2024.02.20 |
Kanban System(간판 시스템, 칸반 시스템) (0) | 2024.02.19 |
[Factory Physics] 8. Variability Basics (1) (1) | 2024.02.12 |
[Factory Physics] 7. Basic Factory Dynamic (0) | 2024.02.05 |