- 본 게시글은 Factory Physics(3e, Wallace J. Hopp) 공부 정리글입니다.
- 개인적인 생각과, 책에 서술되지 않은 내용이 추가되었을 수 있습니다.
- 잘못된 이해에서 비롯된 오류는 지적해 주시면 감사하겠습니다.
Variability Pooling
Variability pooling in supply chain management addresses congestion by combining diverse sources of variability to reduce congestion and optimize efficiency.
Here we discuss how it affects batch processing, safety stock aggregation, and queue sharing.
Batch Processing
A fundamental question arises: Which exhibits greater variability, the process time of an individual part or the process time of a batch of parts?
To answer the question, we must first define variability. As argued in this context, the CV offers a suitable metric for assessing variability.
Consequently, as batch size increases batch process times are less variable than those of individual parts (assuming independence and identical distribution of process times).
This phenomenon occurs because extreme process times for all parts within a batch are improbable, resulting in the batch "average out" the variability of individual parts.
Safety Stock Aggregation
Safety stock aggregation is a strategic approach used in inventory management to consolidate and optimize stock levels across different points in the supply chain.
Here, we learn three key types of stock aggregation: Demand Consolidation, Component Pooling, and Rework Containment.
Demand Consolidation: In Demand Consolidation, the focus is on streamlining safety stock requirements by examining the demand profiles at various nodes in the supply chain. Often, DC(distribution centers) experience erratic demand patterns, high safety stock levels to prevent stock-outs.
However, by establishing a centralized distribution model with modest safety stock buffers at transit points, much of the safety stock can be aggregated back to a central warehouse. This consolidation reduces overall inventory levels.

Component Pooling: Component Pooling involves aggregating variability at the component level rather than at the finished goods SKU level.
By consolidating safety stock requirements at the component level, inventory positions become smoother, leading to smaller stock requirements.

Rework Containment: Rework Containment focuses on consolidating rework management activities to minimize WIP inventory and resource consumption.
In scenarios where multiple factories produce similar products with significant rework requirements, consolidating rework operations to a single site can increase refeed opportunities and reduce WIP inventory through variability pooling.
This consolidation optimizes resource allocation and enhances efficiency in handling, planning, and managing rework activities.

In each of these aggregation approaches, the overarching goal is to optimize inventory levels, improve resource utilization, and enhance overall supply chain efficiency while maintaining customer service levels. Effective implementation requires careful analysis, robust supply chain design, and continuous improvement efforts to reap the full benefits of safety stock aggregation.
Queue Sharing
Queue sharing emerges as a robust method to manage variability in processes involving shared machines or lines. To understand its operation, consider the example of a post office equipped with four customer service agents.
Initially, the office manager established four independent queues, each corresponding to a service agent. However, as time progressed, an increase in customer complaints about prolonged wait times, especially during peak hours, prompted closer scrutiny.
Upon investigation, it became evident that delays were exacerbated when one or two agents faced particularly complex inquiries. Consequently, customers committed to those queues experienced extended waiting periods or resorted to queue-hopping.
In response, the office manager implemented a unified, shared queue system. Now, patrons proceed to the earliest available customer service agent on a first-come, first-served basis, as depicted below. This adjustment optimizes efficiency, reduces wait times, and enhances overall customer satisfaction.

Risk Pooling
In the complex of supply chain management (SCM), where uncertainties hidden around every corner, risk pooling emerges as a beacon of resilience. At its core, risk pooling is a strategic approach aimed at mitigating the impact of variability within the supply chain.
Let's find out Risk Pooling:
- Location Pooling: This involves consolidating inventory across multiple locations or distribution centers. By aggregating demand from various regions or markets, companies can reduce the overall inventory levels required to meet customer demands. This strategy leverages the fact that demands from different locations tend to fluctuate independently, thus smoothing out the overall demand variability.
- Product Pooling: Product pooling entails combining different products within the same inventory pool. By treating similar or complementary products as substitutes for each other, companies can achieve economies of scale and enhance inventory turnover. This approach is particularly effective when demand for individual products is uncertain, as it allows for more flexible allocation of resources.
- Lead Time Pooling: Lead time pooling involves aggregating orders with different lead times into a single pool. By consolidating orders with varying lead times, companies can better utilize their production and distribution capacities, leading to improved efficiency and reduced costs. This approach helps in leveling out the workload and minimizing the impact of fluctuations in lead times.
- Capacity Pooling: Capacity pooling involves consolidating production or distribution capacities across multiple entities or facilities, thereby sharing resources to cope with demand variability and fluctuations in capabilities. For instance, in mixed-model production, capacity pooling allows manufacturers to flexibly allocate resources across different product lines, optimizing efficiency and responsiveness in the supply chain network.
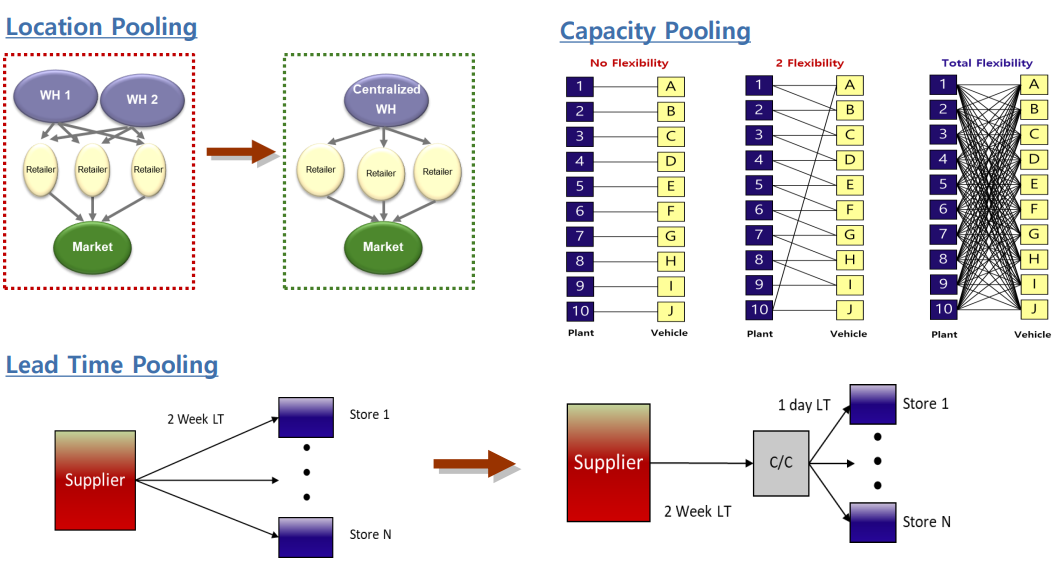
Example: HYUNDAI GLOVIS C/C (Consolidation Center) collects items from subcontractors that provide parts to Hyundai Motors and delivers them to Hyundai Motors at once. This can be seen as an example of lead time pooling.

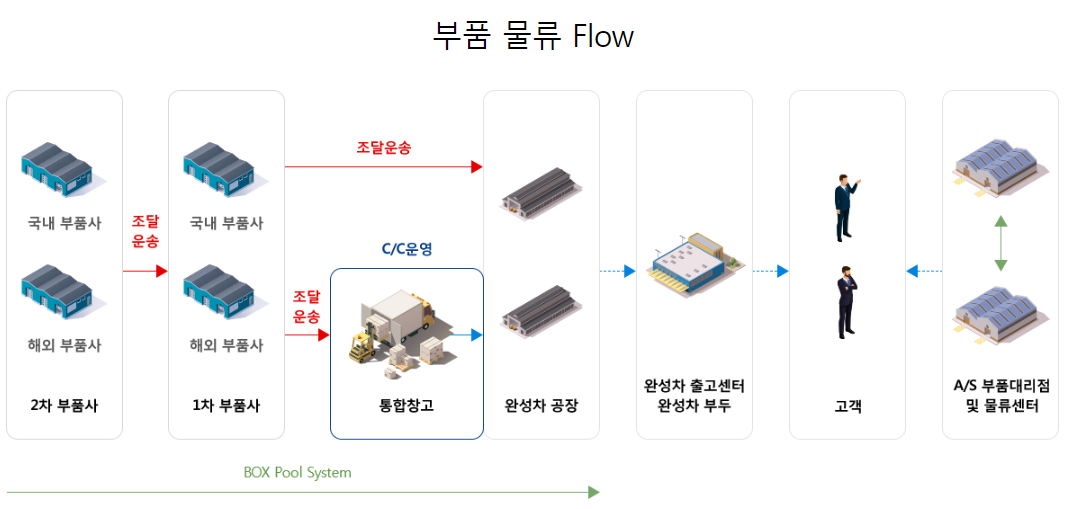
In my opinion, safety stock aggregation in variability pooling appears to be related to location and lead time pooling within risk pooling. If anyone can provide insight into the precise distinction between variability pooling and risk pooling, I would greatly appreciate it. Additionally, if anyone identifies any inaccuracies in my context, please do not hesitate to let me know. Thank you.
참고문헌
HYUNDAI GLOVIS
'공부 정리 > Factory Physics' 카테고리의 다른 글
[Factory Physics] 9. The Corrupting Influence of Variability (0) | 2024.02.21 |
---|---|
[Factory Physics] 8. Variability Basics (2) (0) | 2024.02.20 |
Kanban System(간판 시스템, 칸반 시스템) (0) | 2024.02.19 |
[Factory Physics] 8. Variability Basics (1) (1) | 2024.02.12 |
[Factory Physics] 7. Basic Factory Dynamic (0) | 2024.02.05 |